第8回
株式会社ニッピ機械
青田 崇 氏
7月 2021
株式会社ニッピ機械は、戦後間もない時に創業した老舗で、現在では、日本の皮革産業を支える皮革加工機メーカーとして発展しています。加西市にある本社の周辺には広大な田園風景が広がり、近くには、太平洋戦争時の鶉野飛行場跡もあります。第8回目となるNIROインタビューでは、伝統的な皮革産業を高度な技術で下支えしながらも、新しい分野への挑戦も行っている、ニッピ機械・青田崇社長の想いを伺います。
株式会社ニッピ機械 青田 崇(あおた たかし)様
地元の伝統産業を支え続けて
―― まず、ニッピ機械さんが現在までどのような歴史を辿ってきたか教えていただけますでしょうか。
1947年、私の祖父が姫路に創業した「ニシキミシン商会」が当社の前身で、当時は、お客様の用途に併せて加工したミシンの部品を取り扱っていました。その後、間もなくして、革漉(すき)機の製造を始め、1960年に会社組織「日本皮機製造株式会社」になりました。もともと、姫路は姫路城が築城される前より皮革産業が盛んな所でしたから、皮革加工に使われるミシン(縫製)部品を扱っていた当社が、皮革加工機を取り扱うようになるのは自然な流れだったと思います。かつて、皮革製品は兜や鎧などの武具用が中心でしたが、その後、靴、鞄や財布など消費の裾野が拡がり、量産に対応するため機械化が進みました。その後、1978年に、ここ加西市に会社を移転し、生産設備を増強するとともに製品ラインナップを拡充させ、現在に至ります。このようにして、当社は、姫路の皮革産業の発展とともに歩んで参りました。
―― 「皮革加工」には色々なものがあるのですね。御社のサイトにも詳しく紹介されていますが、その加工の種類の多様さに驚きました。
例えば縫製の前なら、革を所定の形で切り出す「裁断・スリット」、折り返す部分を薄くする「漉き」、折り返す部分への「糊付け」、裁断された革の縁部分を折り返す「折込み」などの工程があり、それぞれに専用の加工機があります。
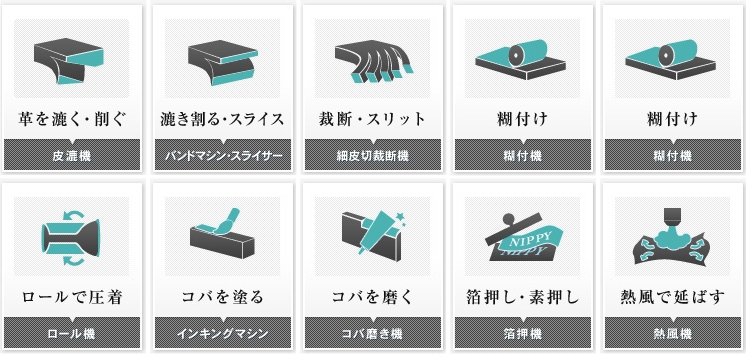
様々な皮革加工
―― この中の「漉き割る」というのは、どういう加工なのですか?
素材を任意の厚さにスライスする加工のことで...ご説明よりも、これを見ていただいた方が良いですね。
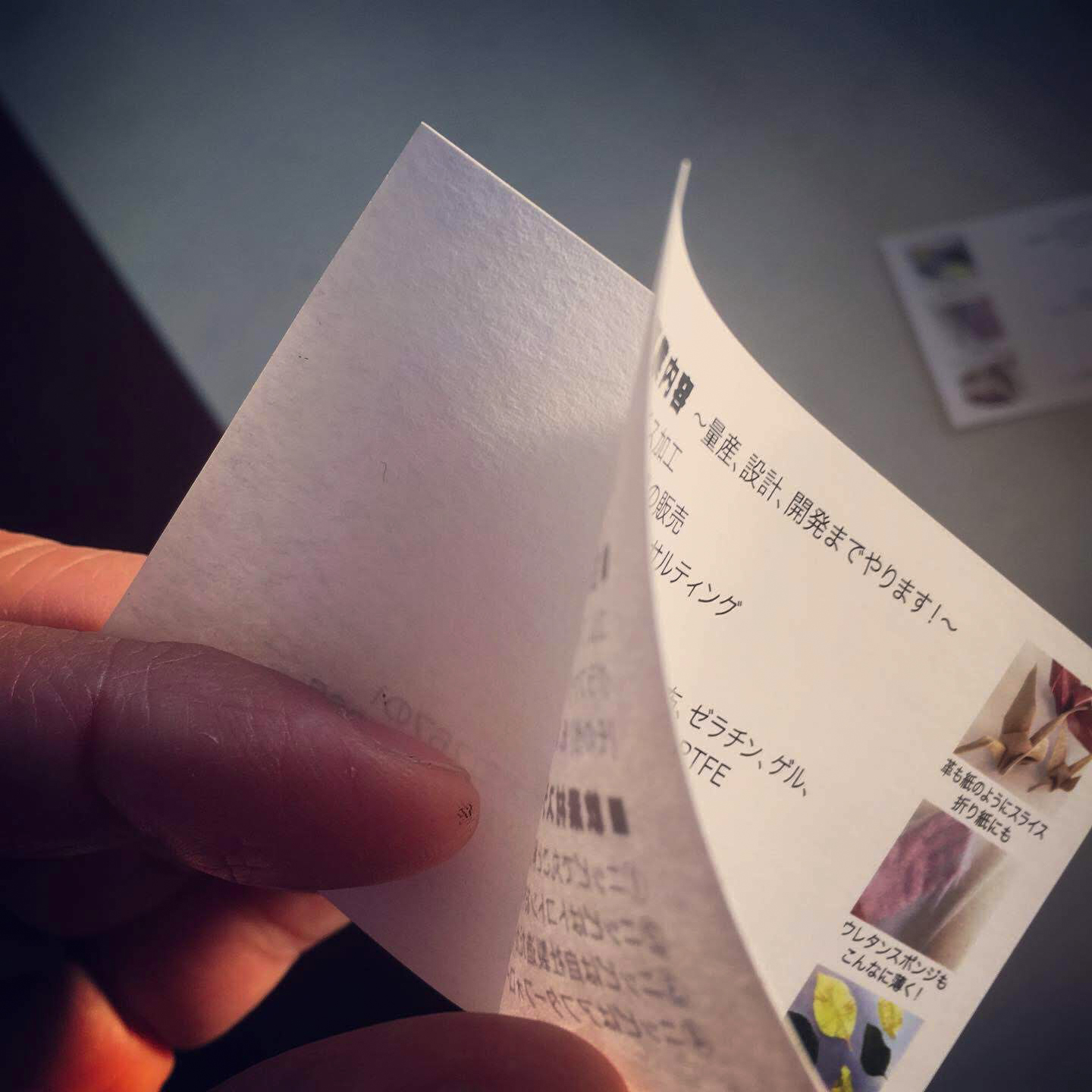
漉き割り機(スライサー)により加工された名刺
―― これは驚きました!社長の名刺がきれいにスライスされていますね。途中で裂けることもなく、均一に加工されています。加工機の精度がどれだけ高いかが良く分かりました。
製品の主な販売先はどのようなところでしょうか?
それは、生産量が圧倒的に多い製靴産業ですね。靴は、まず、紳士用・婦人用という区分があり、パンプス、ブーツなどの種類も様々ですし、四季に応じて履く靴も変わりますから。さらに製造工程も多い。このようにして、加工機も沢山使っていただく必要があります。
―― 靴というと兵庫県では長田ですが。
はい。さらに他に国内で製靴産業が盛んな地域といいますと、東京の浅草、大阪の生野や西成などがあり、多くのお客様に当社の機械をお使いいただいています。
―― 長田というと、阪神淡路大震災の影響があったのではありませんか?
震災もそうですが、リーマン・ショックの影響も甚大でした。もともと、製靴産業は一般消費の冷え込みなどの外部環境に大きく左右されやすい業態なのです。お客様がこのような状況ですから、当然、私達のような皮革加工機メーカーも影響を受け、今では、国内では私達一社だけになってしまいました。
一般消費者向け製品「スカイミニ」の成功
―― 御社が、その高い技術により、皮革産業からの高い信頼と共に成長されて来られたことがよく分かりましたが、その一方で、一般消費者向けとして開発された革漉き(*)機「スカイミニ」が、大きな評判だそうですね。
(*)革漉き:皮革を縫製する前や裁断した後に、素材の淵の部分をスライスして薄くする加工
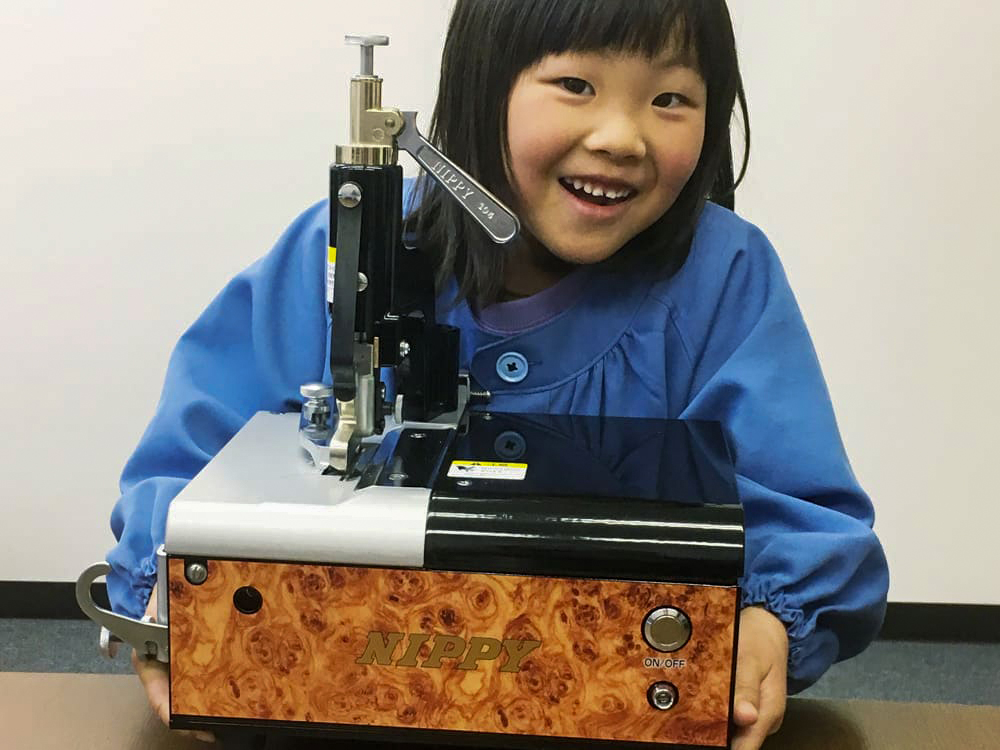
世界一コンパクトな替刃式革漉き機「スカイミニ」
ありがとうございます。この「スカイミニ」、実は2代目なのですよ。初代は約20年前の製品で、「家庭でも気楽に使える革漉き機が欲しい」という、レザークラフト愛好家の皆様の需要に応えるため開発したものです。当時、ホビーユーザーの多くは、革包丁や安価な手動式革漉き機を使っていたのですが、どうしても、加工の効率や品質に問題があったのです。
この初代スカイミニは、旧来の工業用製品をそのまま小型化しましたので、その重量や作業性に課題が残っていました。そもそも「革漉き機」は、丸刃という特殊な形状の刃物を使うなど、100年以上、その原理が全く変わっておらず、この点では初代機も同じだったのです。このように問題は明らかなのですが、なかなか、その解決方法が見つかりません。しかし、ある日、家のテレビで電動髭剃りのCMを見ていてピンと来たのです。「丸刃の代わりに平刃を使ったらどうだろう」と。
翌日の出社早々、技術部門に相談しました。でも、みんな「社長、丸刃をやめるなんて...できっこないですよ」と半信半疑でしたね(笑)。そんな社員達を説き伏せて開発をスタートさせました。新スカイミニでは、従来のように丸刃を回転させるのではなく、平刃を揺動させることで革を漉きます。このように、漉く原理をゼロベースで見直しています。何十年も原理が変わらなかったのは、「丸刃で漉く」というしくみが優れていたからです。そこを変える訳ですから簡単なことではありません。何度も何度も試作を繰り返し、やっと満足できる漉きができるようになりました。
では、スカイミニで、実際に加工してみますね。
―― ああ、これなら私でもすぐに使えそうです!
さらに、新型に加えたゼロからの見直しがもうひとつあります。革は繊維質なので、漉く方式に関わらず、刃は思いのほか早く切れなくなってしまいます。このため従来では、切れなくなった丸刃を、革漉き機に付属した研磨装置を使って研磨する必要がありました。言い換えれば、刃を研磨することが前提なので、革漉き機に研磨装置を付属させることが当たり前だったということです。ところが、この研磨作業の際に大きな騒音と火花が出てしまうのです。これでは、ホビーでレザークラフトを楽しまれているようなお客様に、ご自宅で使っていただくのは難しいですよね。そこで、刃を研磨するのではなく、交換するしくみにしました。こうすることで、従来は革漉き機に付属していた研磨機も不要になるというメリットも生まれます。こうして、A4サイズという小型化・軽量化を実現し、持ち運びも容易になりました。
―― 100年以上も変わっていない原理を変える...これはかなり勇気がいることではなかったですか?
その通りです。業界の皆さんからは「コンセプトは面白けどなぁ」と散々言われましたよ。確かに、工業用製品に比べたら加工速度も遅いですし、性能的には負けるでしょう。でも、メンテフリーで、一定の性能のまま誰でも使っていただけるという大きなメリットを獲得できました。つまり、お客様が真に求めているものは何か、という疑問に応えることができたと思っています。
―― 価格が20万円程度と、ホビー用としては決して安い価格設定とは思わないのですが、2019年の発売以来、既に400台以上を販売されています。これはベストセラーといって良いですね。
はい。初代機の販売実績が20年かけて200台でしたから、お客様の圧倒的な支持を獲得できたと自負しています。一般のレザークラフト愛好家やセミプロの方、それも、国内だけでなく、欧米、アジアなど世界中のお客様に使っていただいています。また、お客様との繋がりを重視し、SNSを使って製品情報や使い方のヒントなどの発信を積極的に行っています。このように、新スカイミニによって、今までお会いできなかったレザークラフターに、イベントやSNSを通じて触れ合うことができるようになり、開発に携わった社員一同、大変喜んでいます。
この海外への展開に対しては、特許の外国出願 等でNIROさんに支援していただきました。その節は、ありがとうございました。
―― お役に立てて良かったです。そういえば、兵庫県からも表彰されたとか。
はい。「令和元年度 ひょうごNo.1ものづくり大賞」の「選考委員会特別賞」を受賞し、「地場産業の振興への寄与」「兵庫県発の技術として世界に発信した」等の評価をいただきました。
さらに、「地場産業や地域ブランド、ニッチ分野等の新市場を創出する製品・技術」という点が評価されて、近畿経済産業局の「関西ものづくり新撰2021」にも選ばれました。
高度な技術による新規分野への挑戦
―― 新しい分野への挑戦が始まっていると伺いましたが。
先程も申し上げました通り、皮革加工機メーカーという意味では、当社は国内でオンリーワン企業です。しかし、この分野は外部環境の影響を受けやすいため、過去の延長のままで続けていては良くないと常々思っています。そこで、皮革以外の分野で当社の加工技術を使っていただけそうなお客様はいらっしゃらないだろうか、と考え、当社のお客様がどのような材料を加工されているか調べてみたのです。そこで見えてきた材料が、ゴム、スポンジや不織布です。「さて、これはどういうことかな」と考えたのですが、柔らかくて加工し難いという性質においては、これらは皮革と同じであることに気付きました。さらに、軟質材に関する展示会にも当社の機械を出展するなどして、お客様のニーズをお聴きしたところ、軟質材の加工機として、様々な用途に使っていただいていることがわかりました。その一つが、ゴムの試験片加工です。タイヤや電線などの製造では、ダンベル試験といって、製品の一部を切り出して、その部分の強さを検査する必要があります。通常でしたら、素材を試験用の形状に成形して検査することが多いのですが、当社のスライサーを使うことで、実際の製品の任意の箇所から、必要な厚さに精密スライス加工ができます。
―― どれくらい精密に加工できるのですか?
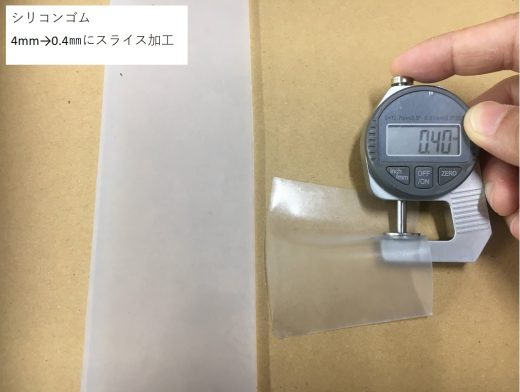
シリコンゴムの極薄スライス加工
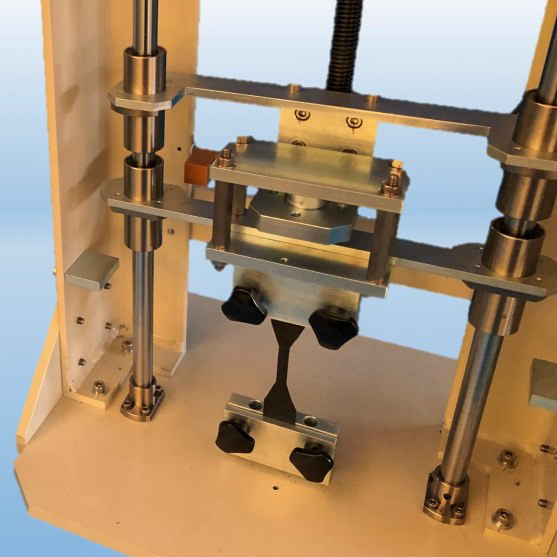
ダンベル試験の様子
例えば、4mm厚というような薄いシリコンゴム素材を、0.4mmの厚さにスライス加工することができます。さらに、従来は加工すること自体が困難であった発泡体のようなものでも0.1mmの厚さに加工できます。また、単に薄くスライスできるということだけでなく、±50μm(0.05mm)という高精度加工ができます。このように、当社のスライサーを使えば、ゴムのような難加工材であっても、薄い素材から、さらに薄く、高精度・高速に試験片を切り出すことができるのです。
―― それは凄いですね!新分野への展開が楽しみです。
日本の皮革産業の今後に向けて
―― 新分野への取り組みを伺いましたが、今後、皮革産業全体を盛り上げていくには、どのようにしたら良いでしょうか?
日本の皮革製品は、海外製品に対して品質では決して負けていません。実際、生産されている皆さんもそのように自負されています。しかし、海外メーカーの売り方に追いついていないと思うのです。例えば、デパートの1階は海外のブランド品ばかりですよね。私達が出展している皮革関連展示会でも、海外勢は、競合企業も合わせて一国で纏めた総合展示の形で出展されたりしていますが、一方で、日本は企業毎にバラバラです。そうではなくて、海外ブランドに対する「メイド・イン・ジャパン」としてのPR方法を考えていく必要があるのではないでしょうか?
―― 御社は、皮革製品そのものではなくて加工機のメーカーですが、どんな取り組みができそうですか?
加工機によって自動化を推進することで、皮革製品のさらなる生産性向上を進めることができます。実際、欧州の高級ブランドメーカーでは、バッグの生産自動化により高い収益力を獲得しています。一方で、国内のお客様には「品質を守るためには手作りが良いのだ」という考え方が根強く残っています。しかし、人手不足や職人の高齢化が進んでおり、自動化の流れは止められないと思うのです。私達としては、自動化が比較的容易な革財布などの「平もの」から初めて、現場の自動化に貢献していきたいと考えており、展示会や弊社のwebサイトなどを通じて、当社の高度な加工ソリューションを積極的に提案していきます。
なお、ビジネス的には、日本メーカーだけでなく海外にも目を向けて市場開拓していくことになりますが、私達としては、まずは、共に歩んできた地場の皮革産業を大切にしていきたいですね。
―― 最後にお聞きしたいのですが、このテーブルの上の「折り鶴」ですけど、よく見たら革でできていますね!
お気付きになりましたか(笑)。さらに、ペン・トレイはもちろん、横の観葉植物も全て革製です。どれも、革の表現の可能性を模索するため、うちの社員が作ったものなんですよ。
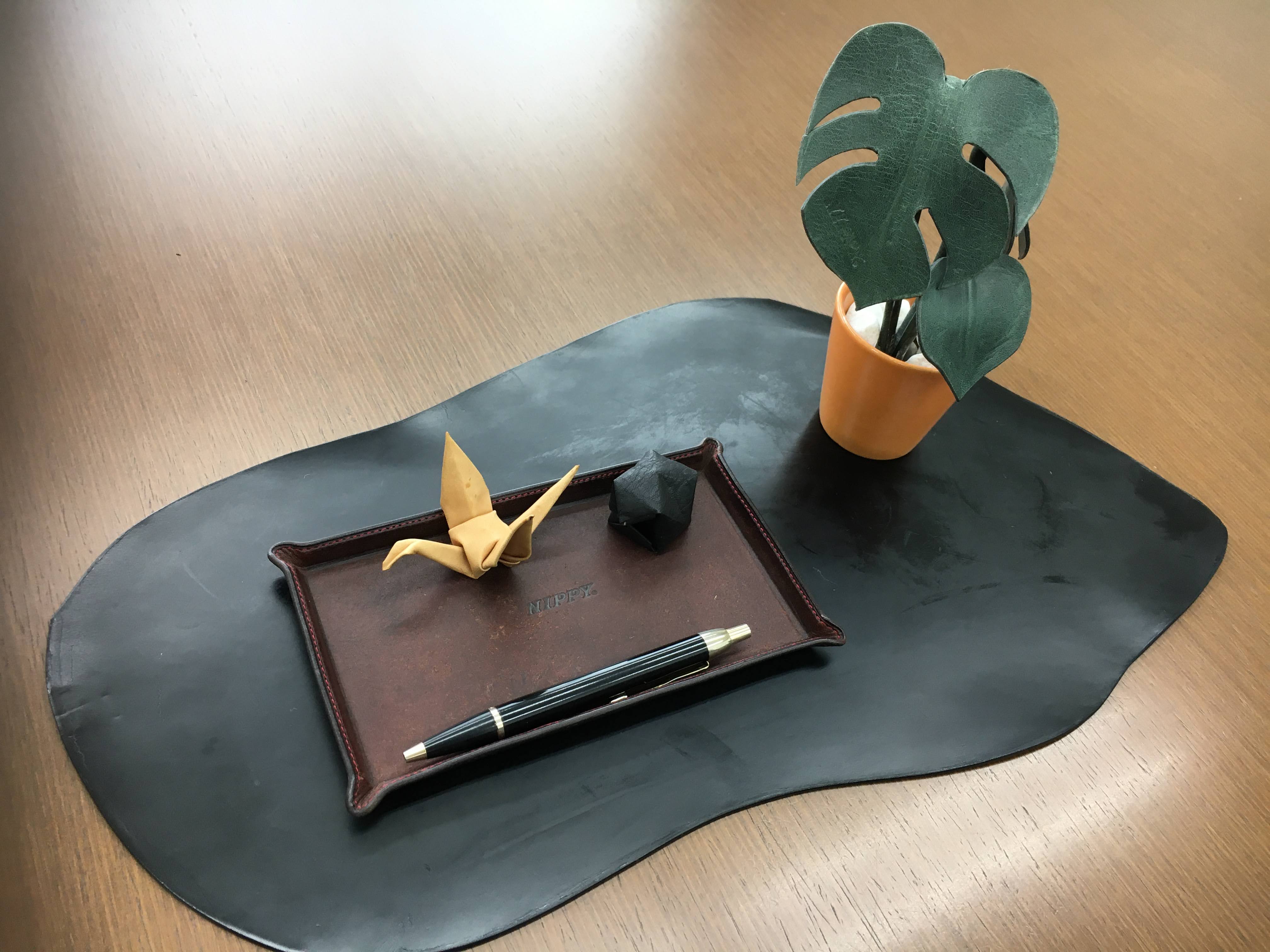
―― やっぱり、そうでしたか!青田社長や社員の皆様の、革に対する愛情が感じられますね。今日は、どうもありがとうございました。
こちらこそ、どうもありがとうございました。